A team of South Korean researchers has designed a lithium-metal battery capable of instantly suppressing combustion processes. By Stewart Burnett
While electric vehicles (EVs) are touted as having many benefits over their traditional gasoline-powered counterparts, mass market buyers are yet to be fully convinced by the technology. A Deloitte survey from 2024 revealed that 29-32% of consumers across the US, Germany, and Japan were concerned about the safety of EV batteries. In China and India, this rose to 38-45%.
EV battery fires are unlike those of internal combustion engine vehicles. A single overheated cell can trigger a chain reaction, causing neighbouring cells to overheat and ignite, leading to a self-sustaining fire that is difficult to suppress. This can burn at extremely high temperatures—up to 2,700 degrees Celsius—and release toxic and flammable gasses, posing a hazard to firefighters and the environment.
Automakers and suppliers have deployed various methods of mitigating fire risk, ranging from machine learning-driven analysis of sensor data to water mist suppression systems. However, South Korea’s Daegu Gyeongbuk Institute of Science and Technology (DGIST) aims to address the problem at the chemistry level. A team lead by Jae Hyun Kim, Principal Researcher and Professor of Energy Science and Engineering, has created a “breakthrough” lithium-metal battery prototype with a triple-layer solid polymer electrolyte (SPE) designed to minimise the risk of thermal runaway and suppress combustion processes.
It’s in the chemistry
One of the biggest causes of thermal runaway is the formation of dendrites: small, branching structures that sometimes occur during battery charging and discharging. As Kim explains to Automotive World: “Conventional SPEs suffer from low ion conductivity and poor interfacial contact with electrodes, which promotes lithium dendrite growth and therefore increases the risk of short circuits and fire hazards.” The solution was to use a triple-layer SPE instead, featuring a “robust” middle layer that boosts the battery’s mechanical strength. It has a “soft” outer surface on either side that ensures efficient electrode contact, facilitating the easy movement of lithium ions. By doing so, energy transfer rates also increase, thereby preventing the formation of dendrites.
“The triple-layer structure achieved mechanical strength, ion conductivity, and fire safety simultaneously—a significant innovation in material design and engineering,” remarks Kim. At the same time, he acknowledges that dendrite formation is not the only risk factor in triggering EV fires: thermal runaway, mechanical failures, and electrical faults remain substantial problems. He also notes that overcharging a vehicle can generate excessive heat and cause incremental damage to cells.
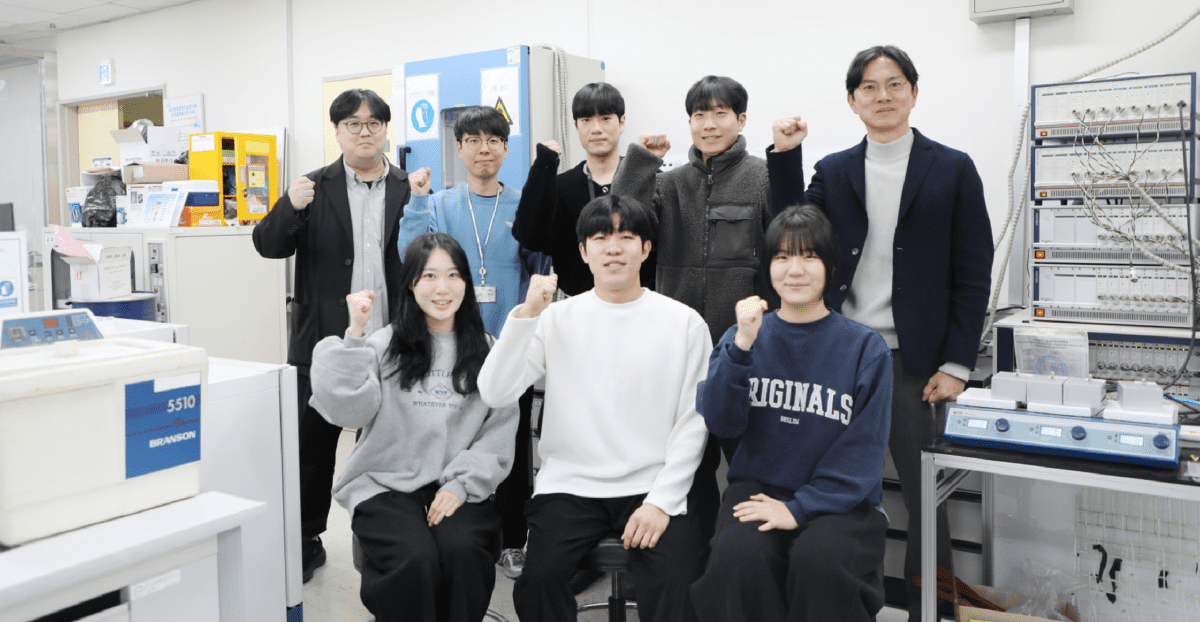
While DGIST’s solution does not address all of these issues at the design level, it can suppress the fires that occur as a result. This is achieved through the use of decabromodiphenyl ethane (DBDPE), a self-extinguishing and flame-retardant additive that the team incorporated into the electrolyte. “When exposed to high temperatures, DBDPE releases bromine radicals, which interfere with the combustion process by interrupting the chain reaction of fire propagation,” Kim explains. “This effectively suppresses flames and prevents the spread of fire, significantly reducing the risk of battery-related thermal runaway accidents.”
He further sheds light on the approach taken: “When we fabricate a triple-layered solid polymer electrolyte, we initially mix beta-zeolite, DBDPE, and lithium salt according to the specified proportions in solvent. After that, we follow a specified fabricating process. This safe and reliable technique can solve the existing risks of fire and explosion due to uncontrolled lithium dendrite growth and the flammability of organic electrolytes in commercialised EV batteries.”
Safety meets functionality
While DGIST’s technology promises to prevent virtually all instances of fire, it does not do so at the expense of a viable, high-performance battery. The research team notes, among other things, that its proposed design boasts strong longevity characteristics, retaining roughly 87.9% of its performance even after 1,000 charging and discharging cycles. For contrast, a typical EV battery will lose between 20% and 30% of its capacity over the same number of cycles.
The longevity does not stem from the same technology that enables fire prevention. Rather, the team is combining two innovations in one battery to demonstrate their compatibility. “They’re basically different mechanisms: DBDPE suppresses combustion, while high concentrations of lithium bis(trifluoromethanesulfonyl)imide improve ionic conductivity and stabilise the solid electrolyte interphase layer, reducing capacity loss during the cycles,” Kim states. By incorporating these various additives into the triple-layer solid electrolyte, he argues that two birds have effectively been killed with one stone.
Commercialisation
“This research is anticipated to make a significant contribution to the realisation of lithium-metal batteries using solid polymer electrolytes,” Kim emphasises. “Our ultimate goal for this technology in particular is commercialisation.” While the team’s research remains at laboratory scale, it is actively working on conducting additional stability tests and refining the electrolyte’s design to accommodate the needs of larger-scale production. To this end, it intends to collaborate with industry partners to transfer the technology into real-world applications, including but not restricted to EVs.
Kim sees potential for the technology’s use in wearables and large-scale energy storage systems intended to boost grid stability. He argues that advancements in battery technology like those offered by DGIST will be key to achieving net zero on several key fronts, including facilitating vehicle-to-grid. However, the immediate focus remains on commercialisation in the EV segment. “The future of the auto industry will be driven as much by safety as by sustainability or electrification,” he concludes. “Our research findings provide a solid foundation for practical implementation in that regard.”